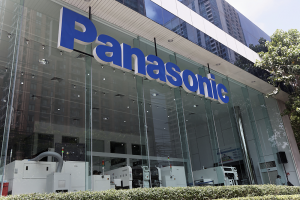
Artificial intelligence (AI) is not only the leading actor in the field of self-driving, it is also indispensable in the development of electric vehicle batteries.
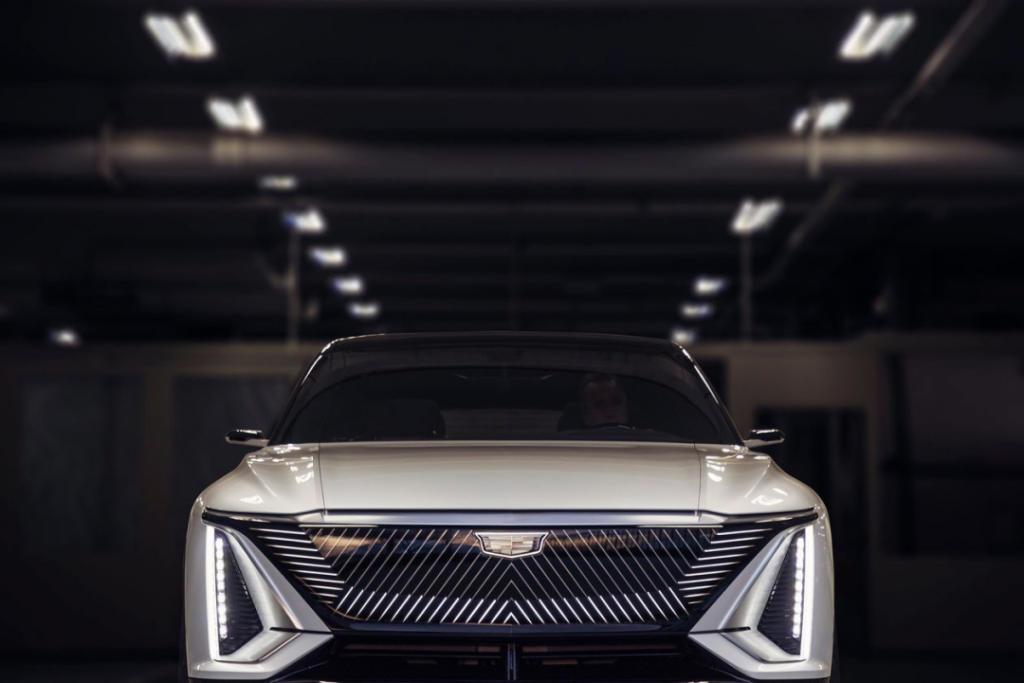
GM Engineering Group Manager Danielle Cory said: “Without artificial intelligence, our electric vehicles would not have powerful charging performance and extended battery life.”
Batteries account for 25% of the total cost of electric vehicles, and half of the cost comes from raw materials. Using artificial intelligence (AI), battery researchers can accelerate the exploration and testing of new materials that may be used in battery production. With the assistance of AI, the progress in research and development is showing unprecedented speed. New discoveries that used to take years to achieve are now possible in a few weeks in some cases.
The researchers said that the battery with which electric vehicle engineers and marketers have strongly requested functional improvements has almost been developed and can be delivered soon. Compared with this generation of lithium-ion batteries that are widely used, the new batteries are safer, faster to charge, and more in line with the concept of sustainability. Experts say that within five years, electric vehicles will reach the same price as traditional internal combustion engine vehicles, thanks in part to the role of artificial intelligence.
How can AI help build better batteries?
In order to achieve faster, safer, and more powerful electric vehicles, battery researchers are using artificial intelligence to speed up the search and testing of high-quality alternative materials.

As shown in the figure, the number 1 represents the Anode, which is responsible for storing lithium and releasing lithium ions when the battery is discharged. The separator allows lithium ions to pass through, while the electrons are forced to travel separately, generating current. AI can help researchers more quickly identify synthetic organic compounds that can improve the Anode’s ability to hold lithium ions.
The number 2 represents the Cathode. When the battery is charged, lithium ions and electrons return to the Anode through their respective paths. With the help of AI, researchers have developed an iodide that can replace cobalt (cobalt is an expensive and difficult to recycle heavy metal used in most lithium-ion batteries).
The number 3 stands for Electrolyte, which is usually a mixture of salt and solvent to promote the movement of lithium ions. With the help of AI, researchers can test new electrolyte formulations faster and determine that increasing the voltage can also increase the flash point (referring to the lowest Temperature that the gas emitted by the volatile substance will flash when it comes into contact with the fire source).
The number 4 represents the Recharge process. Fast charging usually damages the diaphragm, reduces the life of the battery, and may cause a fire. AI helps researchers find the best point to balance charging speed, charging current, charging frequency and battery life.
Time can be shortened from several years to a few days when looking for alternative raw materials of batteries
“Historically, we rely on human intuition and experience to operate and make small changes to things that have worked in the past.”
George Crabtree, Director of the Joint Center for Energy Storage Research established by the U.S. Department of Energy at the Argonne Laboratory at the University of Chicago, said the center aims to accelerate battery research. “Machine learning has increased the speed of this material discovery process by several orders of magnitude.”
To understand the changes that are taking place, look at how current battery research is going. Lithium-ion batteries, a type of battery that packs a lot of energy into small packages, have powered the revolution in home appliances and electric cars.
There are three basic components of lithium-ion batteries, but each component is composed of multiple materials. When scientists want to improve it to reduce costs, improve safety or performance, the possible alternative materials are almost an infinite universe. Before AI, the search for new materials was done through traditional statistical analysis, which was limited by computing power and the ability of researchers to gather information from data.
AI, or machine learning, has changed everything. Fast computers trained to recognize specific patterns are sifting through large amounts of data stored in the cloud, mining material databases, experimental results, and years of scientific literature, and conducting high-energy searches to determine which battery chemistries may perform well and which may fail.
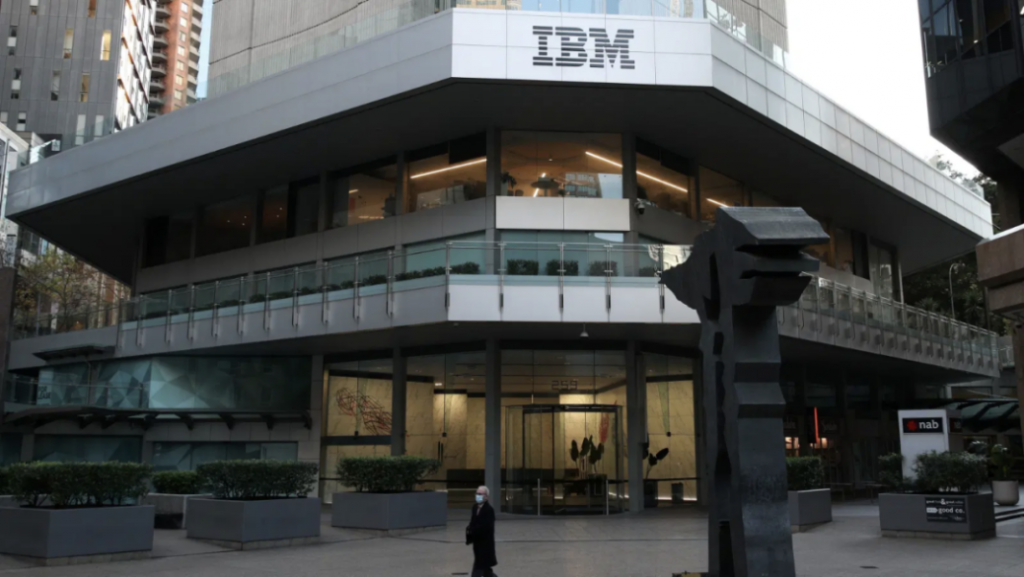
IBM
At IBM’s research laboratory in Almaden, California, scientists use artificial intelligence to accelerate the development of a fast-charging lithium-ion battery that does not contain heavy metals. IBM said that instead of using nickel and cobalt, which are expensive, limited in supply, and difficult to recycle, it has found a way to use iodide materials, which can be obtained from salt water, which may cost the production of such batteries. It is much cheaper than today’s lithium ion formula.
The most recent group of materials that may be used in electrolytes has about 20,000 potential compounds. It may take five years to screen these candidate materials using traditional calculation methods. Machine learning evaluated them within 9 days.
“Artificial intelligence has become more core now, because we adjusted the solvent and electrolyte to make the battery better in terms of capacity and life cycle, because we have more time to train it.” Almaden laboratory director, Jeff Willson said.
Battery test time shortened by six times
In addition to helping material research, artificial intelligence also helps to shorten the test time of experimental batteries. In the past, optimizing the design of a new cell was a process that often took several years to charge and discharge the battery thousands of times. Now, artificial intelligence can quickly analyze the massive data collected during battery testing, allowing scientists to predict performance faster and reduce the number of tests that need to be performed.
At Tesla’s “Battery Day” event, Elon Musk outlined plans for a $25,000 electric car using cheaper and more powerful batteries. The company has set an ambitious goal of producing 20 million electric cars per year.
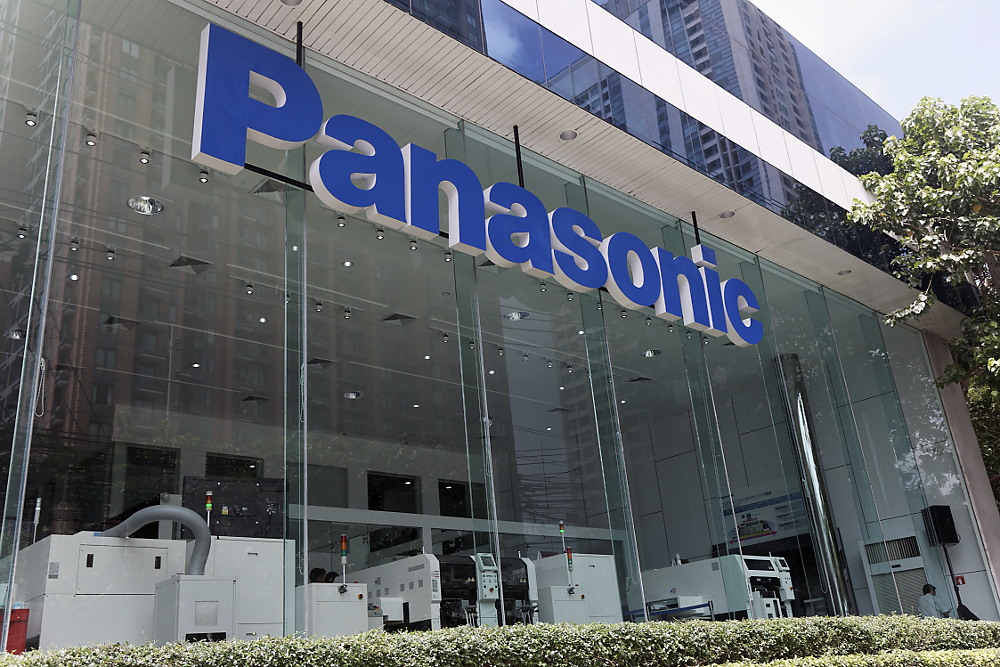
Panasonic
At Panasonic, which produces batteries for Tesla and Ford, the general manager of the company’s Energy Technology Center, said that machine learning has greatly reduced the number of times that batteries must be charged and discharged when testing new designs. “It used to take about three years, now, in the fastest case, it has been reduced to about six months.”
Researchers at StoreDot, a battery manufacturer based in Israel, are using AI to create a battery to cut the charging time of electric vehicles. Depending on conditions and vehicle models, this process may take several hours. Last year, the company’s partners including BP, Daimler AG, TDK and Samsung demonstrated a battery for two-wheeled vehicles that can be charged in five minutes. It hopes to show the battery on four-wheel electric vehicles in 2022.
Research teams from Stanford University, Massachusetts Institute of Technology and Toyota Research Institute are applying AI to determine the best way to charge electric car batteries within 10 minutes to maximize battery life. The traditional method requires 500 days of charging and discharging, but they use a well-trained algorithm to determine the best charging protocol among 224 candidates in 16 days.
William Chueh, associate professor of materials science and engineering at Stanford University and co-author of the study, said: “Our commitment to artificial intelligence is to speed up the development cycle so that we can iterate faster.” The study was published this year in Nature .
At Carnegie Mellon University, machine learning software enabled a robot named Otto to discover a new water-based electrolyte solution with higher performance than the current standard voltage. Otto makes a new mixture of water and four salts every 7 minutes, tests the voltage stability of the mixture, and sends the results to the cloud.
Within 40 hours, Otto used artificial intelligence to find a formula for electrolytes, “better than the most advanced electrolytes.” said Venkat Viswanathan, associate professor of mechanical engineering at Carnegie Mellon University. , He is a co-author of this study. He said it would take years to find the same formula using standard methods.
Comments