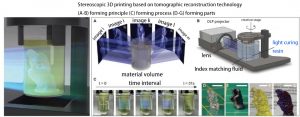
3D printing technology has been more and more deeply into human life.
The principle of 3D printing is actually the same as that of ordinary printers we are familiar with. Ordinary printers can print the text and charts in the computer on a piece of white paper.
When you zoom in on these text charts, you can see that they are composed of tiny colored ink dots. We call these dots pixels.
If these pixels are “printed” on the upper and lower, left and right, front and rear surfaces with three nozzles at the same time, what effect will be obtained? 3D printing is the crystallization of this idea.
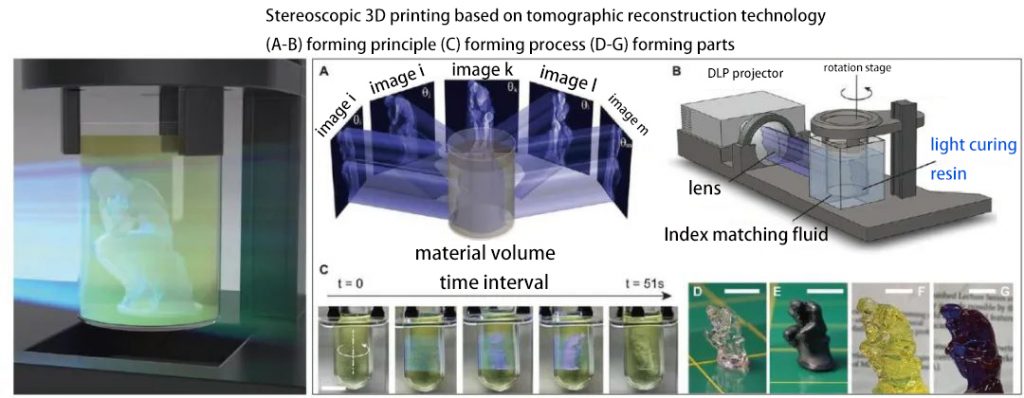
Similarly, the finished product to be printed is designed in the computer and then transmitted to the 3D printer. Each pixel is “stacked on a thin layer of paper” like the computer, and then these objects are finally separated into a thin layer of paper.
Of course, the composition of these “pixels” is no longer ink, but the corresponding raw materials are selected according to the real object. The earliest raw material is plastic.
People can print all kinds of plastic products. Later, the types of raw materials became more and more diverse. The emergence of various materials such as gypsum, nylon, resin, metal and ceramics made 3D printing more worthy of its name.
However, 3D printing still has two difficult problems to solve so far: not fine and time-consuming. Because the printed 3D objects are stacked layer by layer, it is inevitable to have seams or even deviations when stacking, so it is difficult to be as perfect as the integrally formed appliances made by machinery.
Moreover, just as color printing takes longer than black-and-white printing, the more “pixels” you need to eject, the longer it takes. Even if you print a small ornament, 3D printing takes several hours, not to mention other more complex things. How to solve these two big problems?
Using quantum dots, the smallest material that human beings can control so far, as ink for 3D printing may solve the first big problem. Scientists at the Massachusetts Institute of technology in the United States use fluorescent particles to print objects with a volume of about 1 cubic millimeter, with a resolution of 50 nanometers.
If researchers want to make a larger object of about 1 cubic centimeter, the resolution will be reduced to about 500 nanometers. But compared with other 3D printed objects, the 500 nm resolution object is already very fine – its defects can only be seen under a high-performance optical microscope.
Traditional 3D printing technology is like building blocks, stacking raw materials into a whole layer by layer, which is inefficient and time-consuming. If we can use a complete raw material to form a finished product like mechanized production, won’t it greatly improve the efficiency and shorten the time? Several materials scientists at the University of California, Berkeley, came up with this new 3D printing technology: put the raw materials in a container and use the light beam as a “knife” to “carve” the finished products from the solution.
The researchers chose a photosensitive liquid (methacrylate gelatin hydrogel) that selectively solidifies according to the intensity and direction of the light.
When the light is projected from different angles, this multi angle exposure superposition will enable the photosensitive liquid to solidify into a design appearance.
After the design is completed, the researchers project the design drawing with an ordinary projector, and the light beam passes through the picture and shines on a continuously rotating container containing photosensitive liquid.
Slowly, the real object is “carved” out in the solution.
With different design drawings, researchers can make many items, such as toy aircraft, crystal cage balls and even denture models. According to different accuracy and material conditions, the printing time is only 30 ~ 120 seconds.
The highest accuracy of this system can reach 0.3mm at present. It is a potential 3D printing technology that can take into account both time and accuracy.
In the future, with the increase of the types of photosensitive materials, it can print more and more items.
In the further future, this method may also be used to manufacture nanoscale electronic products or robots.
Comments