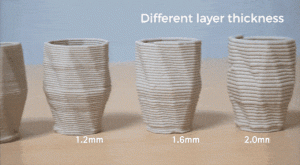
When it comes to 3D printing, what disadvantages do you first think of?
The speed is slow, the accuracy is low, and the printed objects look very fragile.
Now, these shortcomings are not a problem in the face of the latest 3D printing technology.
A team from Germany can now complete a 3D printing in a few seconds, which is ten times faster than the fastest technology before, and the processing accuracy is still very high, reaching 25 microns (less than half the diameter of the hair).
It only takes a few seconds to print a three-dimensional pattern:
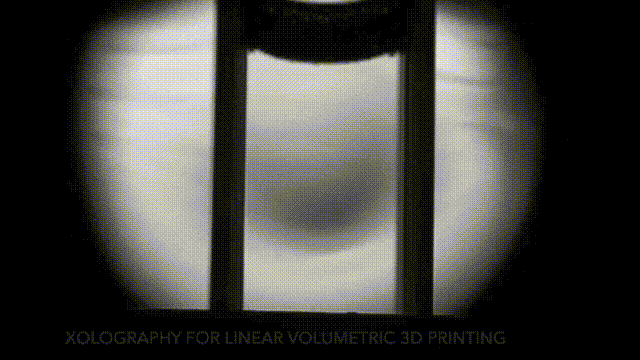
It takes only 68 seconds to print out the Brandenburg Gate, a landmark in Berlin.
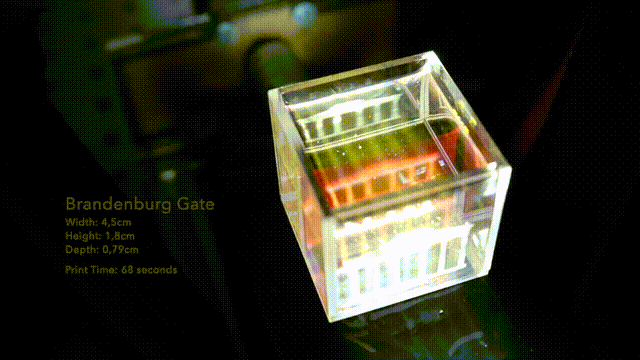
It can even print out the wheels and axles together, which can run without post-assembly.
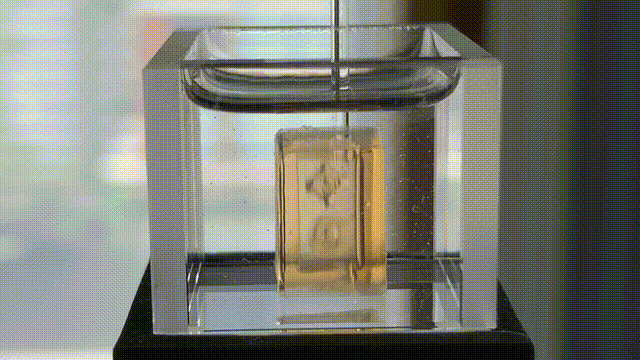
You don’t have to worry about the printed object being too fragile, even if it is hit by a hammer, it will not fall apart easily.
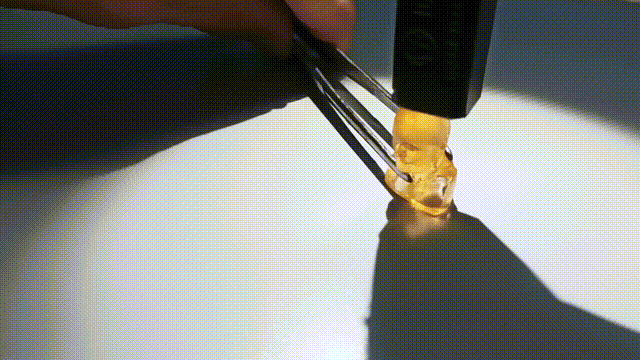
Fast, accurate and stable are the biggest features of this 3D printing technology.
Now, the results of this research are published in the latest issue of Nature.
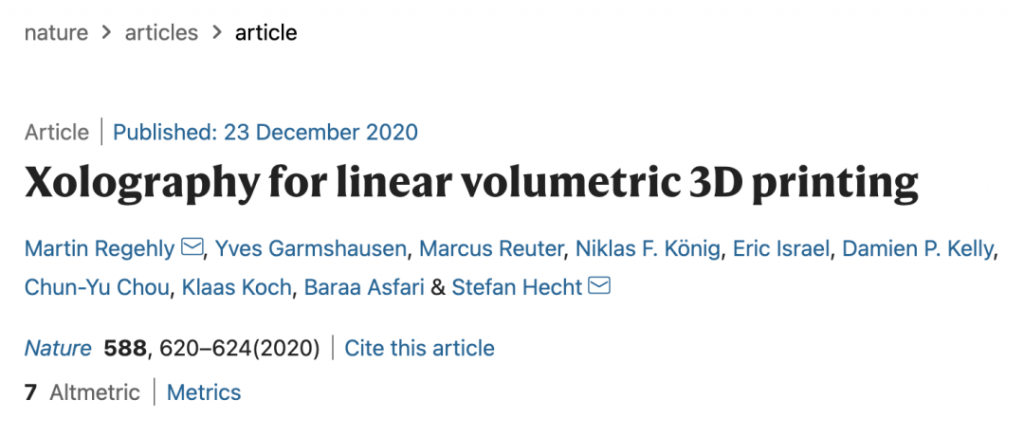
In the movie “Star Trek”, there is a device called a “replicator”. Another object can be copied in a few seconds.
Now due to advances in material science, these science fiction installations may be closer to reality than we thought.
Disadvantages of traditional 3D printing
Why is traditional 3D printing slow? Mainly because you can only print one layer before printing another layer.
Common 3D printers spray resin with nozzles, which are then stacked one after another. Generally, it may take hours or even days to print an object.
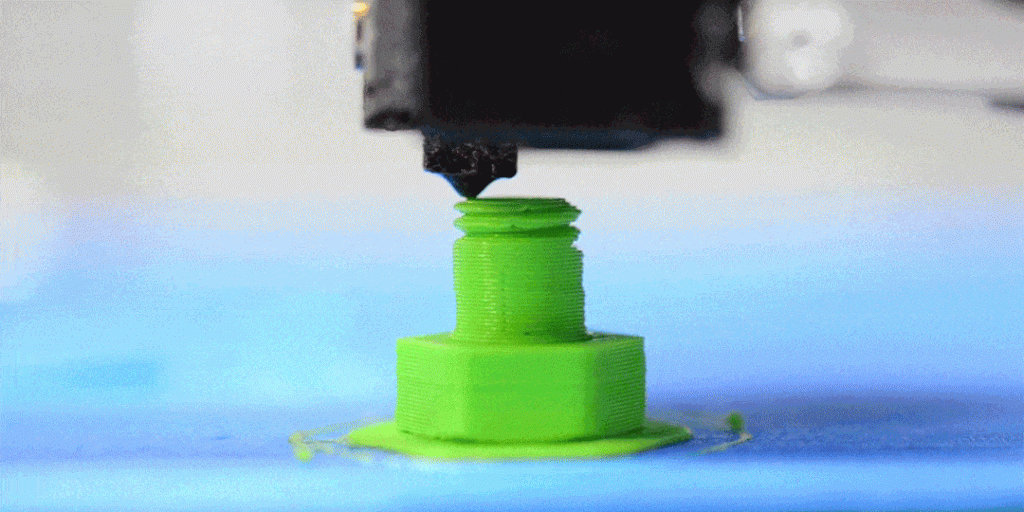
The accuracy of the material printed in this way is affected by the size of the nozzle.
The larger the print head, the low printing accuracy; the smaller the print head, although the accuracy can be improved, the printing speed also slows down.
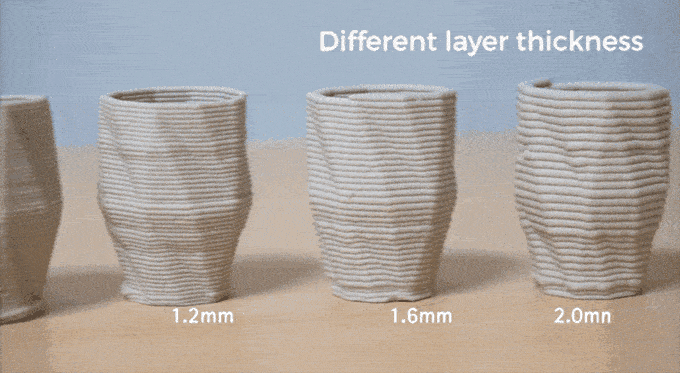
Moreover, this “thousand-layer cake” printing method causes the layer to be not closely combined. From the appearance, the “layering” is very obvious. After receiving external force, the layers are easier to loosen.
After that, a 3D printing startup company called Carbon developed a new technology that greatly increased the speed.
Their paper published in Science in 2015 showed for the first time this technology, called Continuous Liquid Interface Production (CLIP), which can be 100 times faster than traditional 3D printing technology.
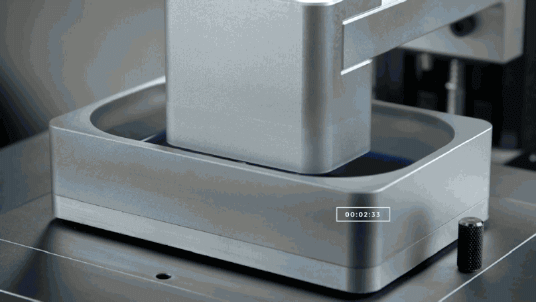
CLIP is fast because it can print one layer at a time.
This technology is like taking a picture, irradiating the surface of the resin liquid with ultraviolet light to cure it. After this layer is cured, pull out the liquid surface and take another cross section until the entire object is printed.
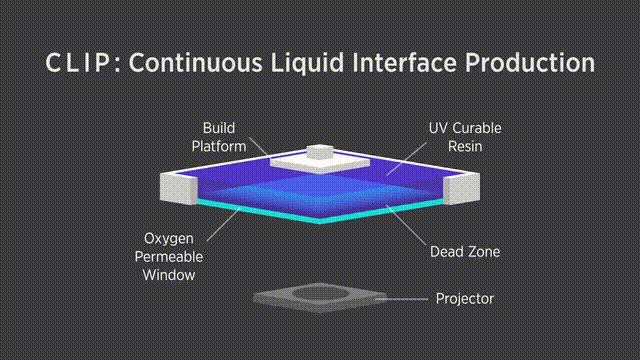
The speed problem is solved, but there is another problem: the printing materials must be integrated.
For example, in the bearings shown at the beginning of the article, the wheels and shafts are separated, and CLIP technology is also incapable. For example, like the “cage ball” below, the previous 3D printing technology is also difficult to cope with.
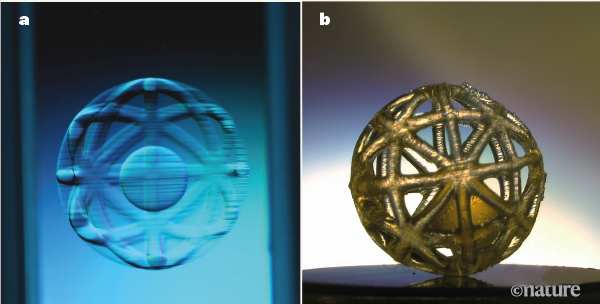
And although the printing speed of CLIP has improved a lot, it is still not enough for mass production. For example, printing a piece of shoe sole still takes tens of minutes.
On the light sheet, use another light to carve
As a result, scientists came up with a new method: use a laser to “carve” the desired object on the liquid.
This kind of liquid can react chemically under light conditions to produce solids.
But if you only use a beam of light to turn the liquid into a solid, it will not print the desired shape well, but will form a straight line:
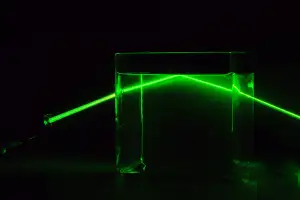
So, how about using the intersection of two beams of light?
If a liquid can produce a solid after two kinds of light reactions, then the intersection can be used to “carve” the desired solid shape in the liquid.
In other words, it is necessary to find a liquid compound that can generate solids after the secondary light reaction.
Now, this liquid compound (dual-color photoinitiator, DCPI) has been found, and its initialization formula looks like this:
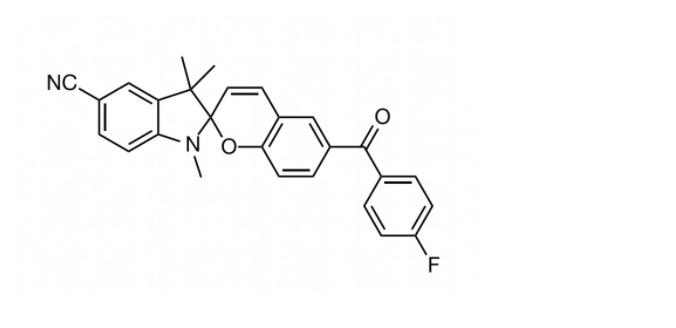
After reacting with 375nm ultraviolet light, it becomes this compound (cyanine state):
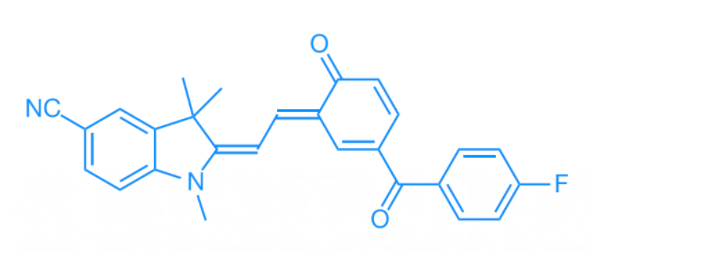
Now, this cyanine compound can react with visible light with a wavelength between 450 and 700 nm to form a solid polymer.
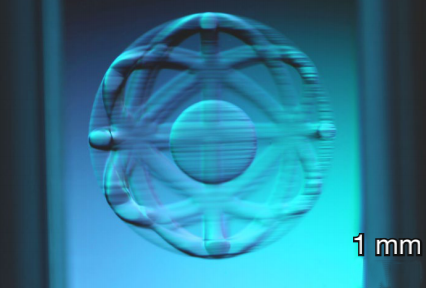
This method is called Xolography, where X stands for “cross” and Holography stands for “holography”, which means to use crossed light to “illuminate” a solid in a liquid.
In addition to the fast reaction speed, the advantage of Xolography is that the cyanine compounds generated by the reaction with ultraviolet light can also be recycled and reused.
The cyanine compound produced in the middle is not stable. If it has not been hit by the second beam of visible light, it will return to the original compound with a heat half-life of t1/2=6s at room temperature, as shown in the figure below.
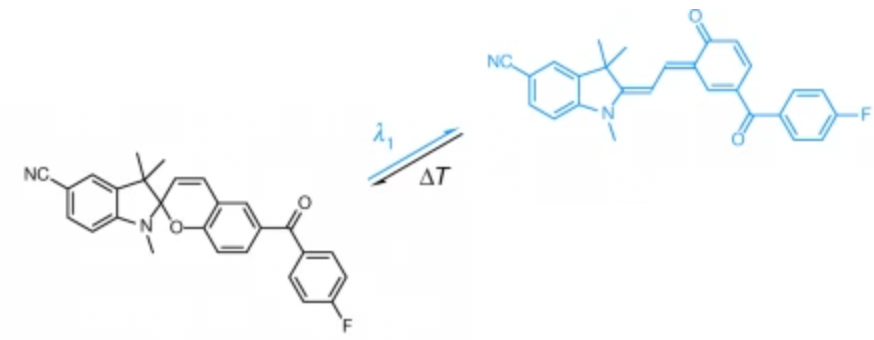
However, the method of directly using two beams of light to cross has a drawback.
The figure below shows the absorbance of the initial compound of DCPI, the reacted cyanine compound, and light of two wavelengths. Among them, the black curve is the initial compound, and the blue curve is the cyanine compound:
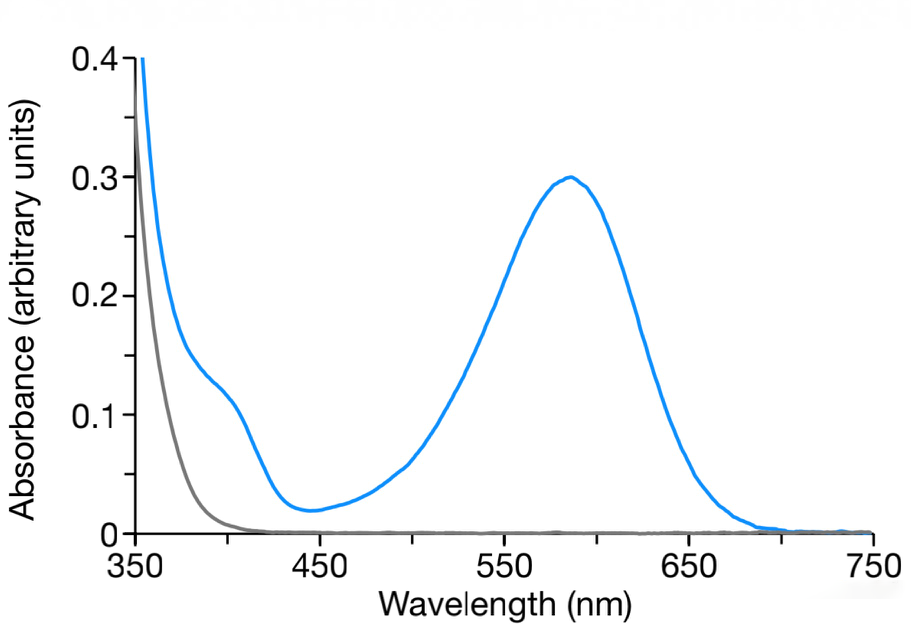
It can be seen from the figure that the cyanine compound can not only react with visible light to form a solid polymer, but also absorb light outside the wavelength of visible light (including ultraviolet light) to produce a photo-initiated reaction.
Therefore, to ensure that this cyanine compound can only be exposed to ultraviolet light once.
In order to achieve this goal, the researchers developed a method called the “light sheet method”, which converts the Gaussian beam of a 375nm diode laser into a divergent laser beam, collimated and focused to the center of the printing volume to form an entire ultraviolet light sheet .
Due to the diffraction of light, the first compound produced will appear “narrow in the middle and wide on both sides” in the liquid (the blue part in the picture):
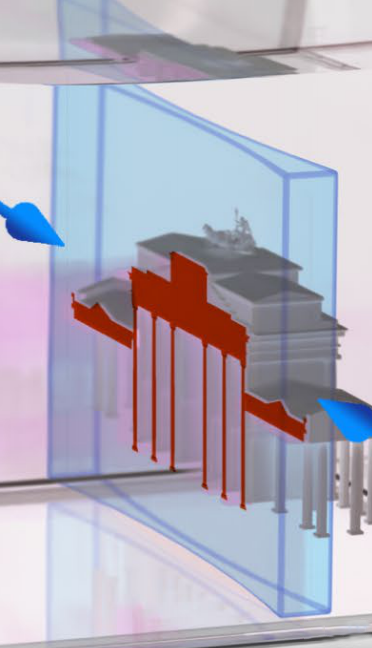
At this time, the visible light is irradiated vertically from the front to form a solid polymer.
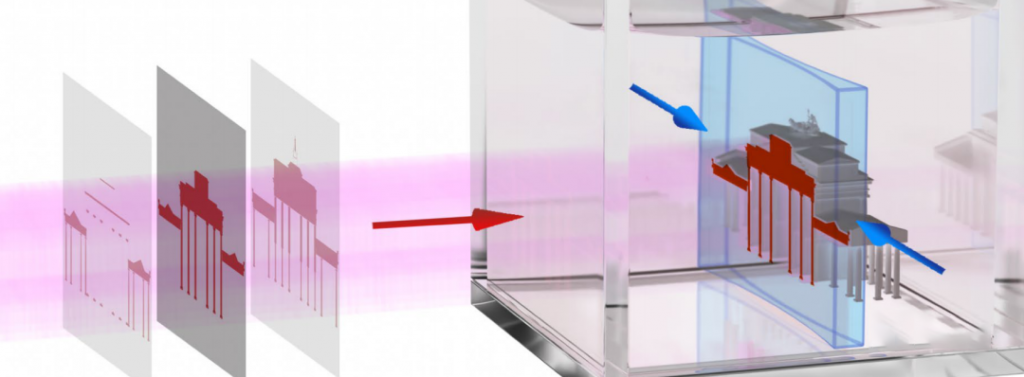
The width of the narrowest part in the middle determines the resolution of this 3D printing technology.
Using this method of “carving on a light sheet with another beam of light”, the unevenness of excitation along the light sheet can be kept below 13%, which is very stable.
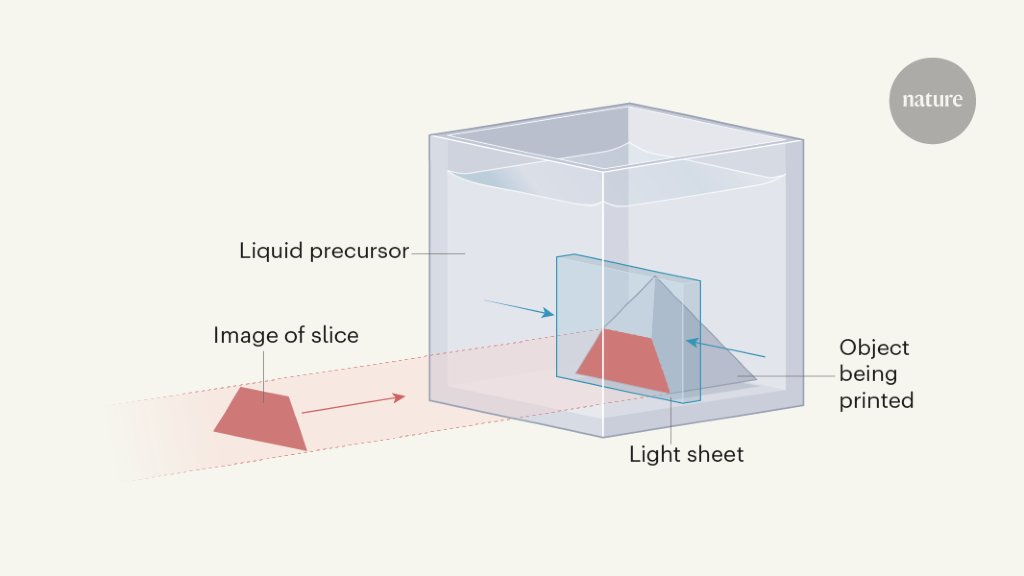
At present, researchers are still optimizing this compound to improve its rapid polymerization ability while ensuring maximum optical transparency and high viscosity.
This magical 3D printing technology was created by many German scientists including Martin Regehly, a physicist at the Brandenburg University of Applied Sciences.
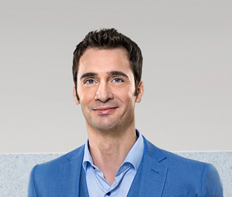
△Martin Regehly
In fact, some people have tried to use the method of crossing two beams of light to perform 3D printing, but they could not achieve the accuracy of this method.
The system program of this technology is written in Python and runs on the Raspberry Pi 4 to control the laser, linear axis and projector. The printing speed and accuracy are quite good, and batch printing is not a problem.
In the future or used to produce running shoes
Of course, Xolography still has certain limitations.
First, the penetration distance of light in the resin is limited, so the volume of the printed object is limited.
Since this method needs to move the resin, if the moving distance in the printing direction is long, the printing time will increase proportionally.
But its ultra-fast printing speed is quite practical. Researchers have thought of using it to process customized sports shoe soles.
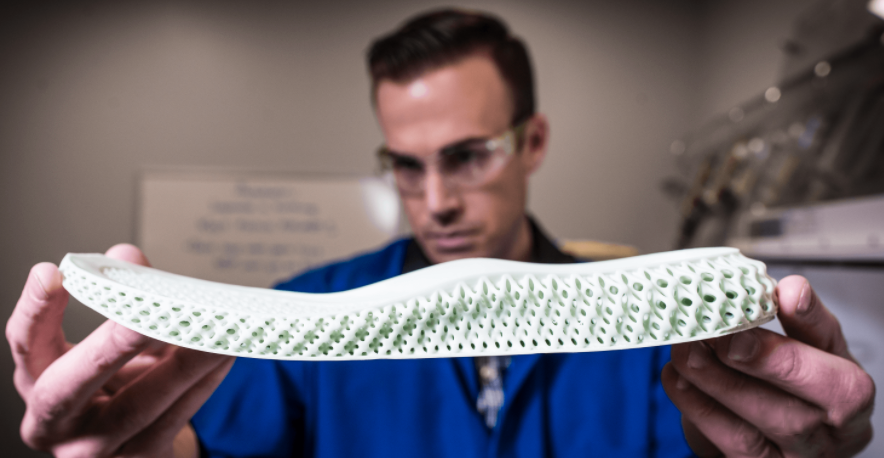
Adidas may think so too.
As early as 2017, Adidas has tried to use 3D printing to process shoe soles. At that time, they used Carbon3D technology to print Futurecraft 4D running shoe soles.
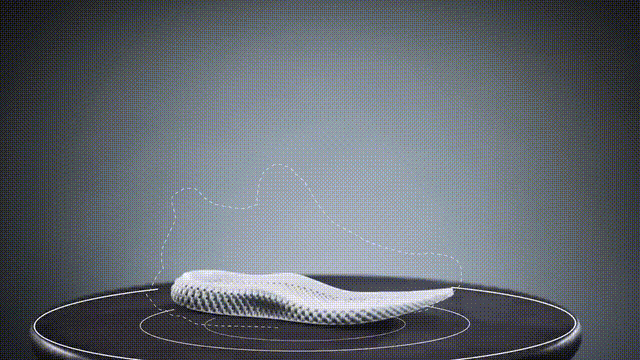
Hollow soles with such complex structures cannot be manufactured by traditional technology and can only be completed by 3D printing.
So Adidas found Carbon to manufacture it, but the process of making a single shoe sole took about 90 minutes. As a result, Adidas produced only about 5,000 pairs of these running shoes in 2017.
If Xolography can be used in 3D printed running shoes in the future, mass production is no longer a dream.
Maybe you can put the latest technology on your feet at a lower price in the future.
Comments