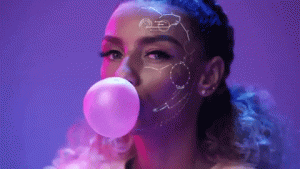
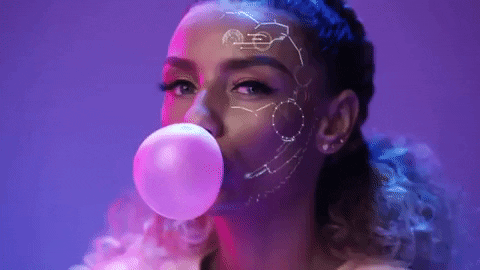
Everyone should have eaten chewing gum. I wonder if you have thought about learning to blow bubbles.
But every time I eat gum, I can’t help but wonder how it is made. Why can’t I chew it?
Later, when I learned the truth, tears came down. It turned out that the relationship between chewing gum and tires was not small. No wonder they were so chewy.
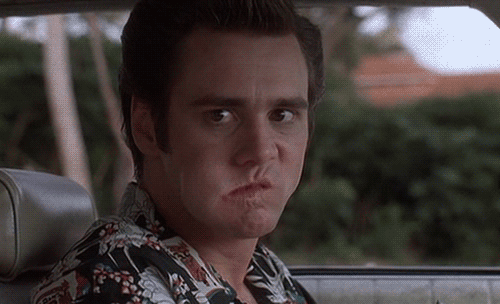
The secret of chewing gum is that it contains gum base. Although the specific formula of gum base is a trade secret, its main components are relatively open.
BBC Documentary Jimmy’s food factory has deciphered in detail how the gum base is made. After reading these ingredient lists, I suddenly feel that I really had courage to chew gum.
This can of colorless and transparent colloid is polyisobutylene, one of the rubber based raw materials, which is generally used to make basketball and tires. But in this state, it can also be chewed directly in the mouth.

Polyvinyl acetate is also one of the important raw materials. It is a kind of plastic products that will become elastic when heated. It is usually used as glue.
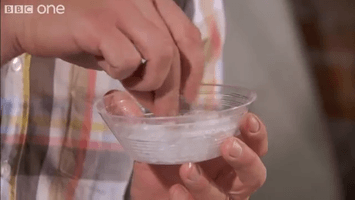
The taste of glue
Put these two things in the pot for heating, stir fry, then add paraffin and pine resin. Sprinkle some talc powder and stir them constantly. Then a hot rubber base can be put out of the pot.
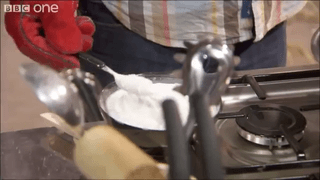
Theoretically, it can be chewed at this time, but the “gum” has no taste and the color is not very good-looking. It is in a very primitive state. It’s soft and easy to swallow by mistake.
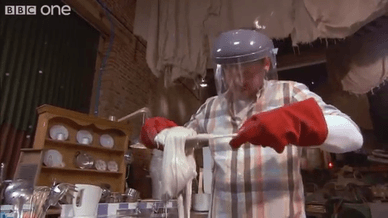
Therefore, many other ingredients need to be added in the chewing gum factory. After multiple production processes, it can be turned into products of various colors and tastes, such as bubble gum, chewing gum and xylitol.
According to the documentary film taken by science channel, we can see that when facing a large number of formed rubber based particles, the first step for workers is to pour the corresponding edible pigment into the rubber based particles according to the final color.
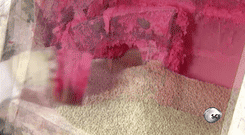
The pigment is poured into the colloidal particles to change the color
In the early days, most bubble gum used pink pigment. The reason is that Frank h. fleer, who first thought of commercial production and sale of bubble gum, only had pink pigment in his factory.
Later, other bubble gum manufacturers also gave full play to the essence of repeaters, most of which borrowed the pink used in the first bubble gum. Then slowly extend some other colors, flavors and shapes of bubble gum.
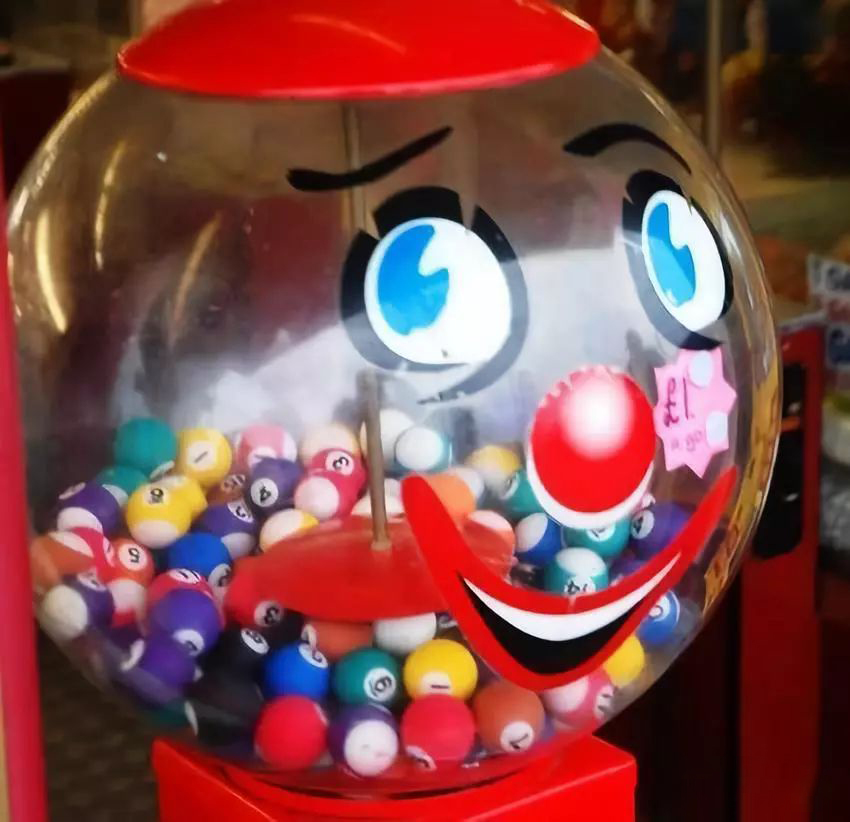
In addition to the change of color, some other ingredients need to be added to the gum to make the originally tasteless gum base more appetizing, so that people are willing to continue chewing.
It’s a good choice to use glucose syrup as a sweetener, and because it’s liquid, you can soak and soften the harder gum based particles.
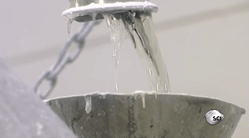
syrup
According to the different products, further adding flavors and other substances, in high temperature environment, the machine mixing these mixtures.
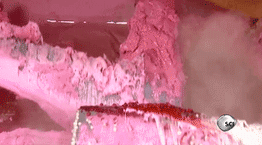
About 20 minutes, the mixture began to take shape, the color gradually became uniform, and the rudiment of chewing gum began to appear. But at this time, the “chewing gum” is still relatively sticky and more sugar oriented, which is not chewy enough.
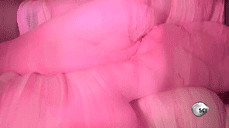
So keep stirring until it’s like foamed dough. There are some bubbles on the surface, and the texture is more flexible. Then you can “get out of the pot”.
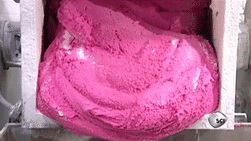
Push the rubber ball onto the pre extrusion press to make it grow into a long strip to prepare for the next extrusion into a specific shape.
Before reaching the next extrusion point, the gum reserves go through a long line, which cools and dries to make it less sticky.
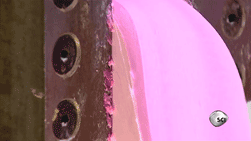
According to the design of each manufacturer, the long bar of gum will be extruded into different shapes. For example, this is made into the shape of a gear.
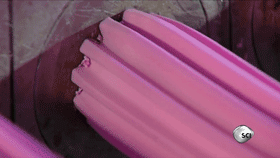
However, it doesn’t mean that the journey of the chewing gum reserve army is over. They need further cooling and air drying, otherwise they will stick to the wrapping paper when packing, and they will be in a mess when eating.
The next stop after extrusion is the special cooling room. The chewing gum strip needs to be cooled at 2-7 ℃ for about 15 minutes.
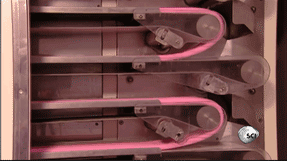
The laminated track can extend the residence time of the chewing gum bar in the cooling chamber, and can also pull and adjust the thickness of the chewing gum to a certain extent.
After cooling, the gum can be cut and packaged, and then placed in containers for sale.
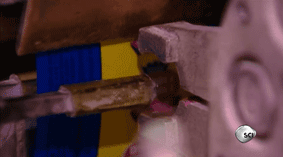
Now we can easily buy all kinds of chewing gum in general supermarkets, convenience stores and grocery stores. But in the past, people gave chewing gum medical meaning, so chewing gum was only sold in pharmacies.
During the World War II, the U.S. military was in short supply of materials. The U.S. military needed to chew gum to calm down on the battlefield. Chewing gum became military supplies. Ordinary people could only buy very rare civilian chewing gum through long lines.
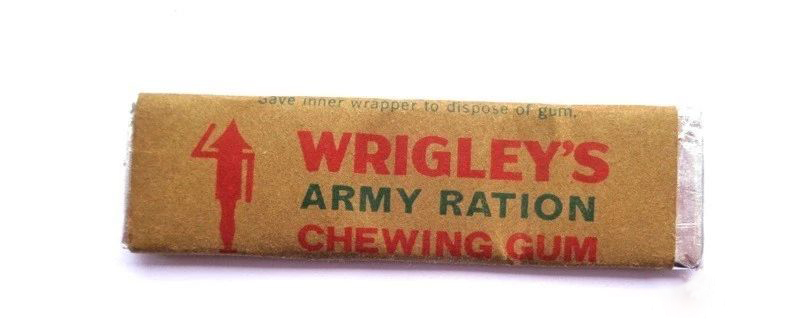
Gum for military use
In wartime, when productivity was insufficient and most of the chewing gum was supplied to the military, it was difficult for ordinary people to buy it from the normal way, so the black market began to sell chewing gum.
In addition, because they are reluctant to throw away the hard to buy gum, they soak it in water and chew it the next day.
Wait, buy someone else’s chewing gum? Do you dare to chew it?
Comments