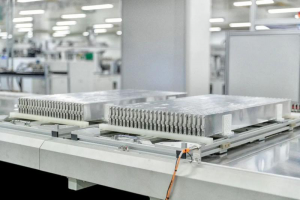
Reducing battery costs is the biggest problem facing the large-scale popularization of electric vehicles and the price approaching fuel vehicles or even lower. Elon Musk, who has always been known as a cost killer, knows this well, and the process of Tesla’s transformation from weak to invincible is Musk’s pursuit of extreme costs.
According to Musk’s statement on Battery Day this year, Tesla started from the first principles and is committed to reducing the cost of the entire battery value chain, including cell design, cell manufacturing, anode materials, cathode materials, and cell integration. Reduce the cost of battery packs by 56% to $60/kWh in 2023.
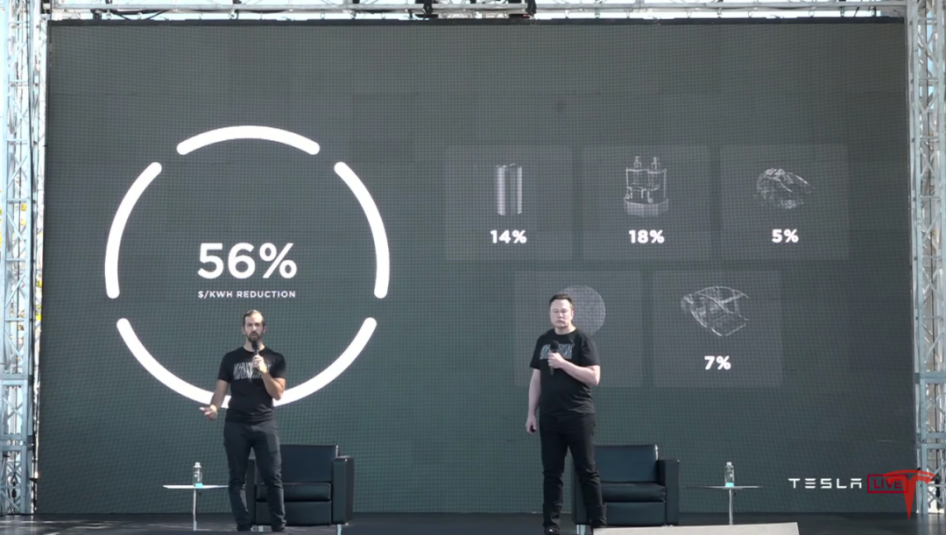
Based on this, the current cost of the Tesla battery pack is about 136 US dollars/kWh, and the industry consensus is that if the price of electric vehicles is to be the same as that of fuel vehicles, the price of battery packs should be less than 100 US dollars/kWh. Looking at it now, Tesla still has a long way to go. However, just as Tesla was still drawing a pie for the public, the price of lithium-ion battery packs in the industry had reached the historical threshold of $100/kWh.
US$100/kWh is here
On December 16, according to Bloomberg NEF (BNEF), the price of lithium-ion battery packs appeared at a historical moment of less than US$100/kWh for the first time this year. This price is created by electric buses from China. BNEF emphasized that although this is the lowest reported price, the actual weighted average price of electric buses in China is slightly higher, reaching US$105/kWh.
If the battery pack and the battery cell are calculated separately, the price of the battery pack is $126/kWh, and the average price of the battery cell is $100/kWh. This shows that the PACK part accounts for 21% of the total price.
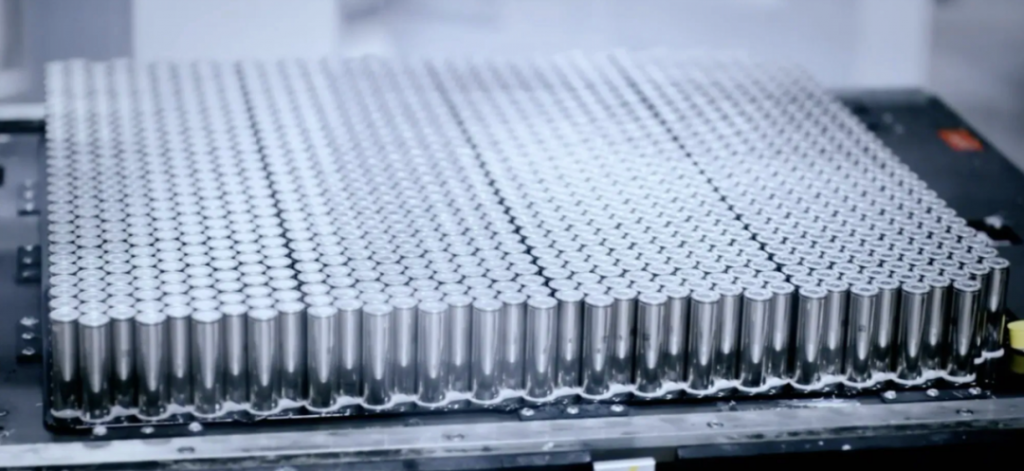
The reason why battery pack prices can be significantly reduced in 2020, BNEF pointed out is because of the increase in orders, the growth of pure electric vehicle sales and the introduction of new battery pack designs.
In addition, the decline in new cathode materials and manufacturing costs will further drive down the price of battery packs in the short term. Another positive factor is that the price of cathode materials has been declining since reaching a high point in the spring of 2018, reaching a more stable level in 2020.
James Frith, BNEF’s head of energy storage research and the lead author of the report, said: “Li-ion battery packs below $100/kWh are a historic milestone. In just a few years, we will see low industry average prices.
At this price, it will be even lower. In addition, our analysis shows that even if the price of raw materials returns to the high point in 2018, it will only postpone the industry average price to $100/kWh by two years.
Keep the industry out of the expected development track. As leading battery manufacturers move up the value chain and invest in cathode production, the industry is becoming more and more adaptable to changes in raw material prices.”
It is reported that the price of lithium-ion battery packs is moving in the direction that people expect. Ten years ago, the price of lithium-ion battery packs was as high as $1,100/kWh, but now it is $137/kWh, a reduction of 89% in 10 years. BNEF’s latest forecast is that by 2023, the industry average price will be close to $100/kWh.
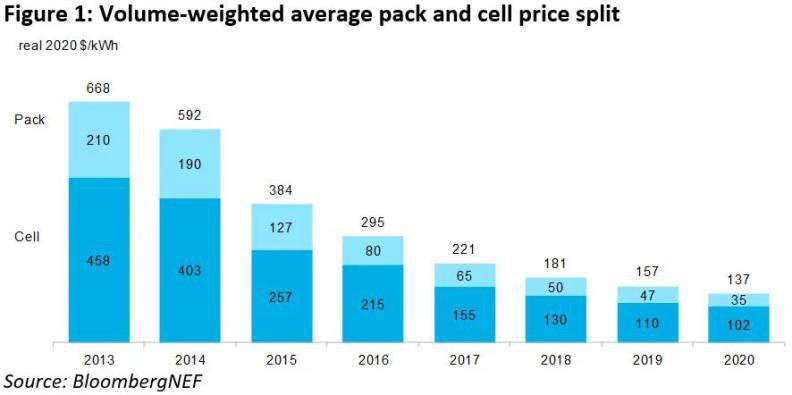
The battery prices investigated by BNEF in 2020 include electric passenger cars, electric buses, electric commercial vehicles and fixed storage applications that can commercialize lithium-ion batteries, and try to cover the entire industry.
The reason for the historical low of $100/kWh is also based on the industry-wide survey results of BNEF. Therefore, BNEF predicts that by 2023, the average price of battery packs will be $101/kWh.
Near this critical point, automakers should be able to produce and sell electric vehicles for the mass market at the same price and profit margin as fuel vehicles. It should be pointed out that the forecast does not include government subsidies.
There is no doubt that the leading battery manufacturers that have emerged in recent years are the most important reason for the continued decline in battery prices. It is understood that leading battery manufacturers now have a gross profit margin of up to 20%, and the utilization rate of their factories exceeds 85%.
Therefore, maintaining high utilization is the key to lowering the price of batteries and battery packs. Because if the utilization rate is low, the depreciation cost of equipment and plant will make the battery cost per kilowatt hour higher.
And when the battery market is not a monopoly, but a competitive landscape where many are competing for the world, diversified battery raw material routes are also an effective way to reduce costs. BNEF Senior Energy Storage Assistant Li Daixin said: “The increasingly diversified raw materials used in the market have led to a wide range of price batteries.
For example, battery manufacturers are racing to adopt some new raw materials, such as lithium nickel manganese cobalt oxide (NMC (9.5 .5)) and lithium nickel manganese cobalt aluminum oxide (NMCA). These new formulations will be mass-produced as early as 2021. However, neither formulation can match the cost advantage of lithium iron phosphate (LFP). The lowest battery price that led to the report was only $80/kWh.”
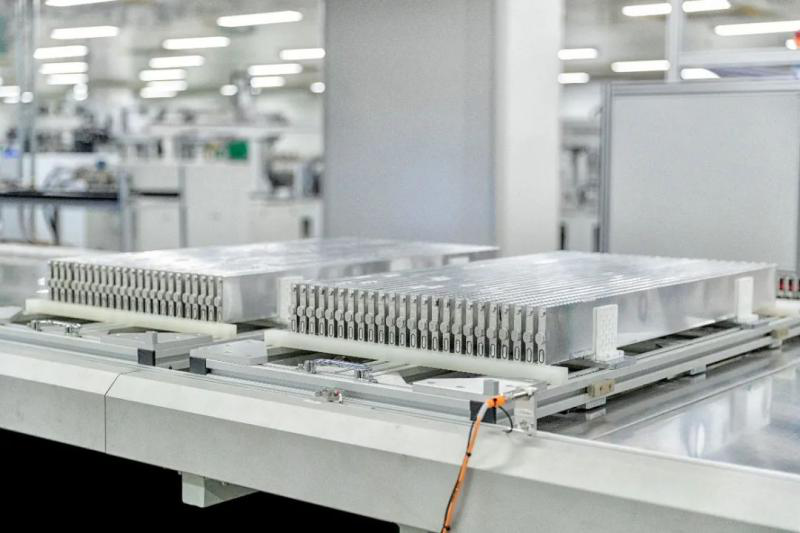
Therefore, the industry’s prediction that the price will reach $101/kWh by 2023 is likely to become a reality. However, the 2030 expectations from $100 /kWh to $58/kWh will greatly increase the uncertainty.
This is because the existing chemical formula is difficult to achieve this, perhaps only the solid-state batteries that have started to become popular in recent years can achieve this.
BNEF predicts that when solid-state batteries begin mass production, their manufacturing costs will be about 40% of current lithium-ion batteries. These reduced costs mainly come from raw material supply and production cost savings, as well as production equipment and high energy density cathode materials.
And if these price cuts are to be achieved, a supply chain of key materials that have not been used in lithium-ion batteries, such as a solid electrolyte supply chain, needs to be established.
So, when will such a cheap solid-state battery be installed in a car?
Getting in the car in 2021?
According to Nikkei News, Japan has begun to accelerate the commercialization of all-solid-state batteries through a joint government and corporate approach. Among them, Toyota’s goal is to push solid-state batteries from the laboratory to practical scenarios earlier than any other car company.
The initial plan is to publicly trial-produce all-solid-state battery electric vehicles in 2021, and then carry out a series of performance tests. Toyota Motor is the industry leader in the field of solid-state batteries. It has thousands of patents in this field, and the number of patents ranks first in the world.
The biggest difference of solid-state batteries is that the current liquid electrolyte in lithium-ion batteries is turned into solid electrolyte, which greatly reduces the risk of battery fire risk and effectively improves battery safety.
The biggest advantage of solid-state batteries is that the energy density is several times that of lithium-ion batteries, while the charging time is only about one-third of the current pure electric vehicles. If the current pure electric vehicle can recharge 300 kilometers in 15 minutes, then the future solid-state battery electric vehicle will only take 5 minutes.
Moreover, compared with lithium-ion batteries of the same size, the battery life of solid-state batteries can be more than doubled. At present, the battery life of mainstream electric vehicles is mostly about 500 kilometers, so 1,000 kilometers can be easily achieved in the future.
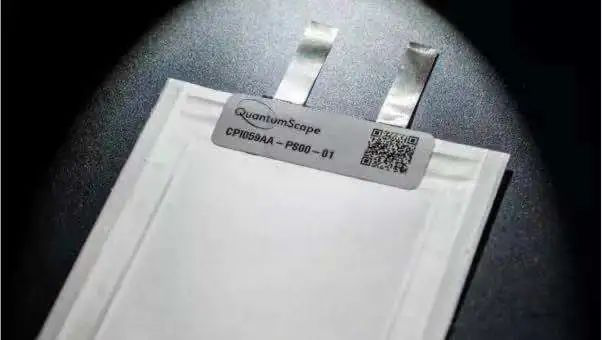
It can be said that when solid-state batteries really usher in large-scale loading, that is the point in time when fuel vehicles really withdraw from the stage of history.
The entire industry is currently accelerating this point in time. The Japanese government is discussing a supply chain production system around solid-state batteries and will provide hundreds of billions of yen in subsidies for this purpose.
And Japanese companies have also begun to take action. For example, Mitsui Metals will put into production equipment at a research institute in Saitama Prefecture, Japan, to produce solid electrolyte materials.
It is expected to reach an annual output of tens of tons in 2021 to meet the company’s trial production level of orders.
Outside Japan, China and Europe have also begun to deploy solid-state batteries for commercial applications. Volkswagen is not hesitating to embrace solid-state battery start-ups, hoping to meet the huge battery demand it needs in the next few years.
Volkswagen’s plan is to establish a mass production line of solid-state batteries by 2025. Not only Volkswagen, but almost all industries are exploring the commercialization of solid-state batteries, including Daimler, Ford, BMW, Toyota, and other international car companies, Supply chain players such as Samsung, Panasonic, Ganfeng Lithium, Huineng, Ningde Era, etc., are exploring the industrialization of solid-state batteries.
According to incomplete statistics, a total of 46 companies worldwide are focusing on the research and development of solid-state batteries.
Therefore, whether it is to reduce the price of existing lithium-ion battery packs, or to make solid-state batteries known as the killer of fuel vehicles. They all point to a certain future, that is, electric vehicles will eventually become the mainstream, and the countdown to the withdrawal of fuel vehicles from the stage of history is about to begin.
Comments