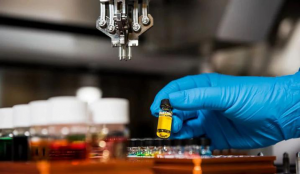
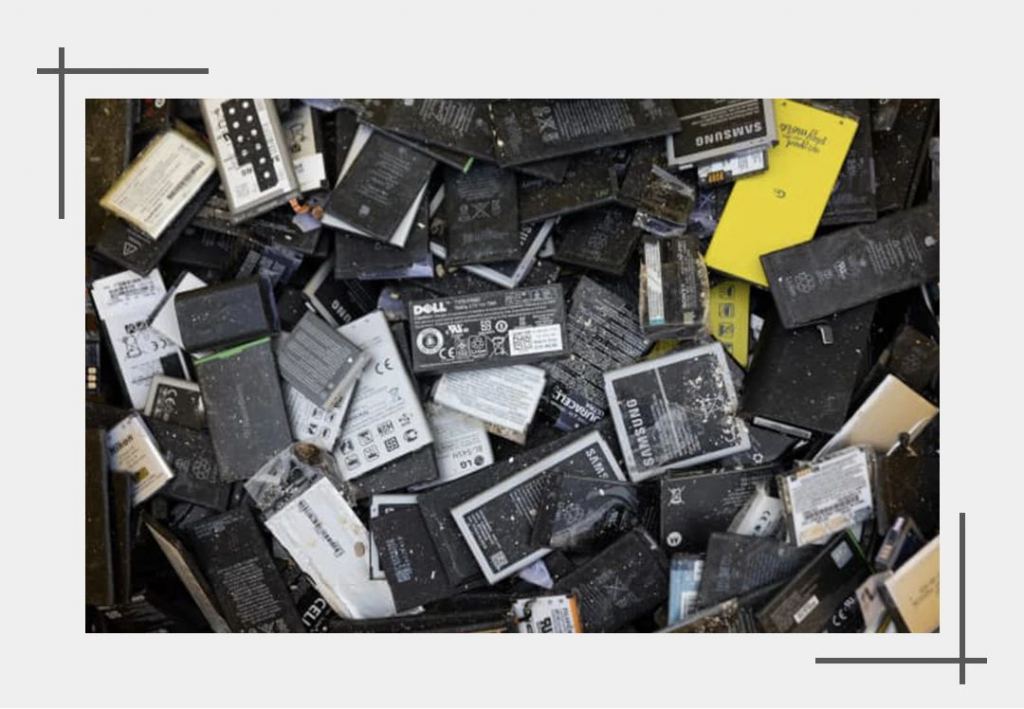
Inside every smartphone and tablet, there is a heavy brick with a dark and complicated history: the battery.
The lithium in the battery may come from salt flats in South America, where there are some of the driest areas in the world where several months of evaporation consume millions of tons of water.
The cobalt in the battery may come from the Democratic Republic of Congo, where children are said to be killed or maimed while extracting cobalt from the ground. Collecting various atoms and assembling them into a working battery may require thousands of people from more than a dozen countries. Then, after several years of use, the used batteries are usually thrown into landfills and incinerators.
As lithium-ion batteries leap from handheld devices into cars, trucks and homes, entrepreneurs and scholars are racing to find ways to reuse these precious materials. Investors bet millions of dollars on Redwood Materials in Nevada, which can mine metals from e-waste.
Its competitor Li-Cycle is committed to solving the logistics problems of battery transportation. Some other companies are developing a technology that can rejuvenate the battery without completely damaging it.
By solving this problem from all aspects, these teams are working towards one goal: to turn depleted batteries into valuable resources.
Tim Johnston, co-founder and executive chairman of Li-Cycle, said: “We spend all our money on making batteries, making chemicals, and then burning them at the end of the cycle. This is incorrect.”
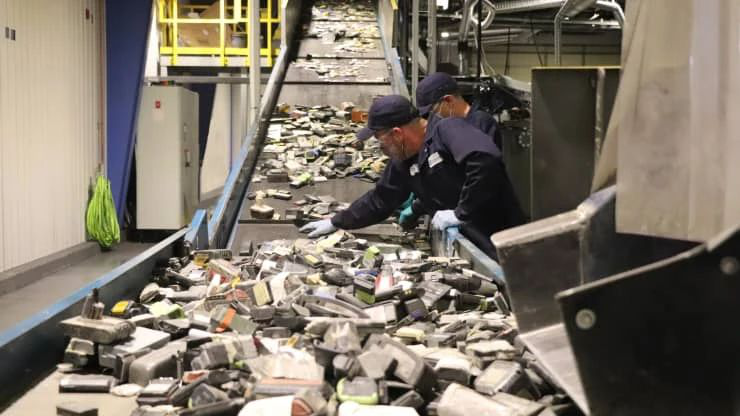
Industry insiders are both excited and apprehensive about the upcoming battery “tsunami”. According to Ajay Kochharr, co-founder and president of Li-Cycle, more than 500,000 tons of lithium batteries have been discarded worldwide, most of which are small electronic products.
However, as the world transitions to an electricity economy, it is expected that by 2030, the world’s demand for lithium-ion batteries will increase 10 times. Most of the explosive growth of lithium-ion batteries will be driven by electric vehicles, which carry batteries weighing more than 1,000 pounds. “We are at the tip of the iceberg.” Kochharr said.
Kochharr and others see this problem as an opportunity to replace the fragile and problematic supply chain with a more “recyclable” system that uses the materials of the previous generation of batteries to make an integrated battery. They don’t recycle for the sake of recycling.
According to Statista, by 2030, the annual value of the lithium-ion battery recycling market alone may reach 18 billion US dollars, and in 2019 this figure was 1.5 billion US dollars.
The recycling startup of Tesla co-founders
One of the leading start-ups in the US market is Redwood Materials, which is the latest investment project of Tesla co-founder J.B. Straubel.
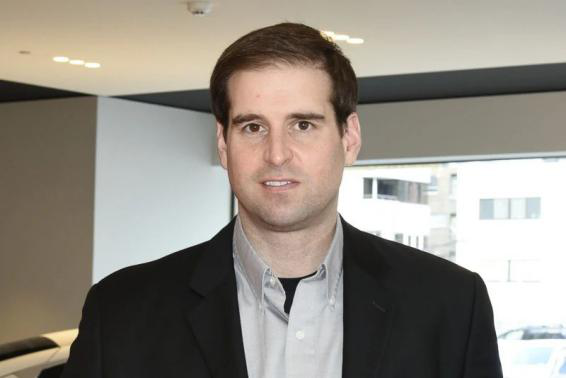
During his 16 years as Tesla’s chief technology officer, Straubel realized that he had no plans to process these cars after their useful life. Unlike mobile phones, a half-ton car battery cannot be left unused in the trash drawer.
Most electric vehicles are currently in their heyday, but in the next five years, early electric vehicles will begin to be eliminated in large numbers, and a tsunami will be set off.
Since its establishment in 2017, Redwood Materials has been preparing for the first wave.
The start-up is located in Carson City, and currently has two factories that process all waste and defective batteries produced by the nearby Tesla Super Factory.
The Tesla Gigafactory is jointly owned by Panasonic and Tesla. The Panasonic Scrap Factory alone provides about 1 billion watts of materials each year, and the other 12 partners also provide similar amounts, which amounts to about 20,000 tons of materials per year. The company also recently partnered with retail giant Amazon to handle batteries from Amazon.
From battery to atom
After classifying the newly arrived batteries, Redwood Materials used a patented process, including burning the battery, melting the contents of the battery, and then immersing it in a liquid to extract the required elements (although the specific procedure is based on the battery type Tailored).
A spokesperson for the company said that ultimately, this technology can recover 95% to 98% of nickel, cobalt, aluminum, graphite and more than 80% of lithium in batteries.
Most of these materials are sold back to Panasonic for the manufacture of new Tesla batteries.
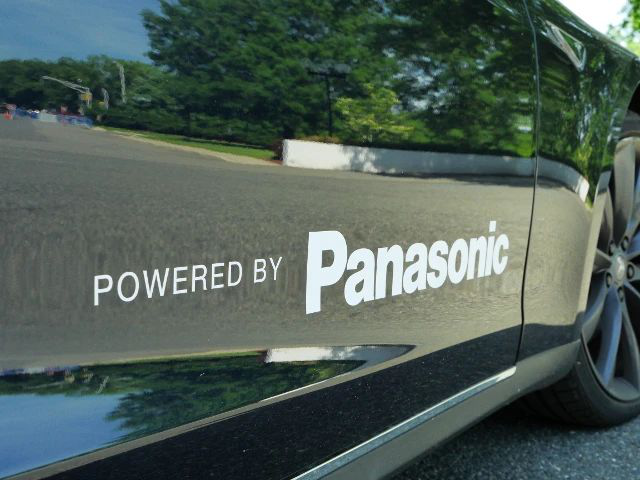
“Redwood Materials has assembled an excellent team to work with us to handle a wide range of waste streams and develop raw materials, which we can then use in our battery manufacturing process.” Said Celina Mikolajczak, vice president of battery technology at Panasonic Energy.
With funding of US$40 million from Capricorn Investment Group and Breakthrough Energy Investment Corporation, the company is currently working to increase the production capacity of the Carson City plant.
Breakthrough Energy Investment is an environmental investment fund that includes Amazon founder Jeff Bezos and Microsoft co-founder Bill Gates.
“Spoke” mode
Johnston and Kochhar founded Li-Cycle in a similar way and launched it in 2016. Before that, they worked together at Hatch, a global engineering company specializing in battery chemicals. They build their business around the “center and spoke” model.
Since batteries are a fire hazard, the cost of safe transportation may be high. In order to reduce the distance, Li-Cycle intends to collect the battery in the local “spoke” equipment, dividing the battery into three parts: plastic casing, mixed metal (such as foil) and active materials, such as cobalt and nickel at the core of the battery-a kind of Black dust called “black clumps”.
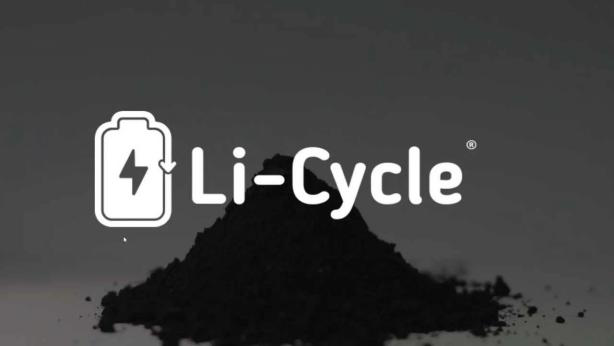
Li-Cycle can sell these materials directly, or ship the black clumps to a “central” factory and soak them in liquid at room temperature. Johnston said that this can extract metals—even lithium—with 90% to 95% efficiency. Many processing methods are difficult to effectively capture lithium.
The company currently has two “spokes” in operation, one in Ontario, Canada, and the other in Rochester, New York, which can decompose a total of 10,000 tons of lithium-ion batteries each year.
Li-Cycle recently announced plans to establish their first “center” in Rochester.
Starting at the end of 2022, the center will be able to separate 25,000 tons of agglomerates (from 65,000 tons of batteries) into lithium, cobalt, nickel and other elements each year. Like Redwood Materials, the company hopes to expand as soon as possible, and has raised approximately $50 million in funding.
“This is a lot of space, we need a recycling team.” Kochhar said.
Revitalizer
But looking ahead, the researchers pointed out that the long-term profits of removing the atomic part of the battery may be very meager. The chemical structure of the battery changes every year.
For example, Panasonic reduced the cobalt content in Tesla batteries by 60% between 2012 and 2018. These changes may require constant adjustments to the recycling process while also reducing its profitability (cobalt is the most expensive and most valuable battery component).
A more effective method may be to recycle batteries at a higher level, recycling their larger molecular structures instead of atoms. Chemist Steve Sloop, the founder of battery research company OnTo Technology, compares batteries to apartment buildings.
Instead of tearing it down for wood and brick, why not renovate it? He said: “Batteries have invested a lot of energy in manufacturing. We are working hard to save this investment.”
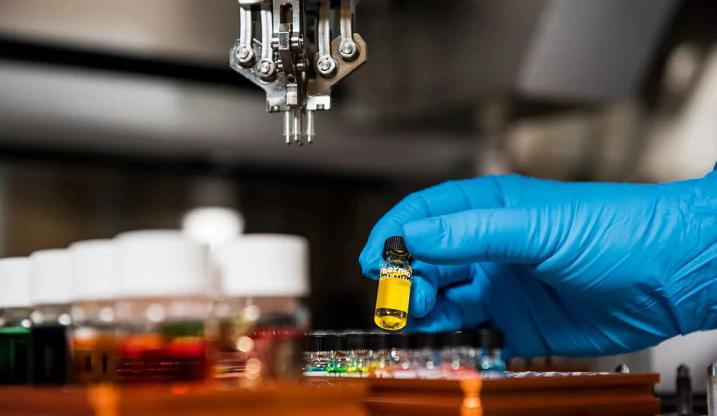
In the case of lithium-ion batteries, this means replacing lithium, because every time it is charged and discharged, a small portion of lithium is attached to the battery’s molecular holder. When the free flowing lithium in the battery is exhausted, the battery is dead.
In September last year, Sloop published a case study describing how his laboratory automatically disassembled and crushed recycled Apple batteries, soaking the active material in a lithium-rich bath to restore it to its original state.
The final product marks the first full fuel cell reassembled from industrial raw materials.
OnTo Technology is just an organization pursuing a “direct recycling” strategy. The Department of Energy funded a research consortium called the ReCell Center, which also supports similar projects.
According to Linda Gaines, a transportation systems analyst at the Argonne National Laboratory who led the work, the center is currently organizing a different type of “relithiation” informal competition to see which one works best.
“Relithiation has come a long way,” she said. “This is indeed a stage where we can consider scaling up.”
Scale up will be the main challenge for all these initiatives. In the laboratory, it is relatively easy to reduce batteries to atoms or replace lithium.
But how to collect, transport, sort, disassemble, process and redistribute the upcoming millions of tons of materials is a difficult problem.
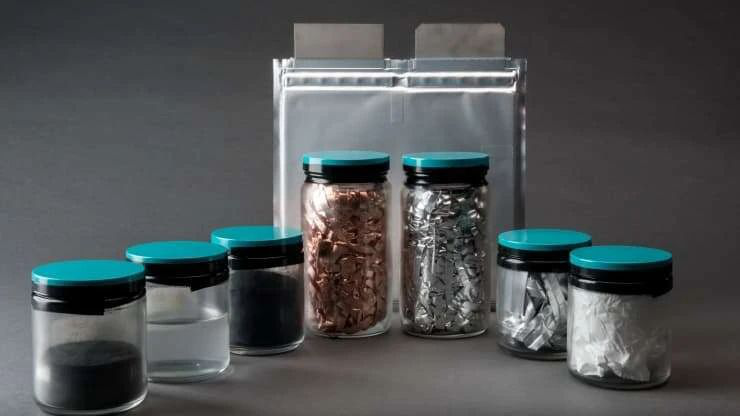
“This is a new technology that will be available soon.” said Gavin Harper, a materials scientist at the University of Birmingham, who participated in the British battery recycling project ReLib. “We have not seen the problems, challenges and opportunities it will bring.”
Multinational recycling network
In Europe, the demand for legal international collection and recycling solutions for electric vehicle batteries is increasing. Now, leading battery collection companies from Belgium, Germany, Italy, the Netherlands and Norway have jointly established Reneos SCE as a multinational network.
The founding companies of Reneos SCE include Belgium bebat, GRS Batterien Service GmbH in Germany, Cobat in Italy, BatteriRetur in Norway and Stibat in the Netherlands.
Through their new European platform, they provide cross-border collection, transportation, storage, reuse, reprocessing or recycling of disassembled electric vehicle batteries, all in compliance with the laws of various countries.
“Recycle, reuse or take it away directly and deliver it to the customer’s chosen location. All these institutions can collect batteries in all European countries, store them, disassemble them, and then dispose of them.
For this purpose, we have our own partners; We can also work with our customers’ preferred partners. Customers can closely track everything through the “Tracking and trajectory” system.” Reneos CEO Philippe Celis explained.
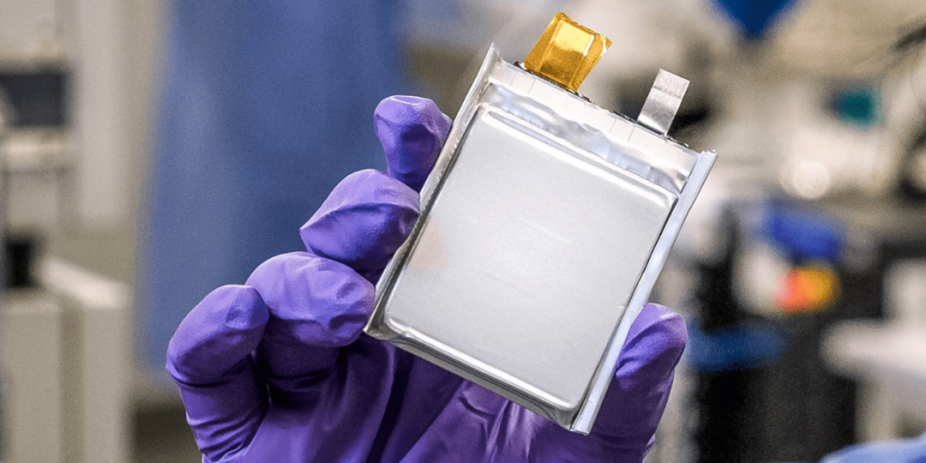
These partners collect lithium batteries from lithium batteries for electric vehicles, industrial and private use. “With Reneos, we can provide safe solutions for our international operations customers, not only in Germany, but throughout Europe.
I am not just referring to legal safety, but the safety of the entire recycling, transportation and recycling process.”
Reneos CEO Celis added: “By bringing together leading experts, we are making Europe a center for battery recycling and enhancing our competitiveness against Asia and the United States.” From an industry perspective, he said the initiative Attracted a lot of interest.
For example, in October 2019, Reneos took over the collection and recycling of used batteries for Zero motorcycles. The electric motorcycle manufacturer has authorized dealers in the Benelux, Austria, Czech Republic, Finland, France, Germany, Ireland, Italy, Norway, Portugal, Spain, Sweden and the United Kingdom.
Reneos partners in various countries can collect, transport and process batteries in these countries in accordance with their respective laws and safety regulations.
Comments